APQP(高度製品品質計画)フェーズ、例
APQP(アドバンスド製品品質計画), スペインの "Advanced Product Quality Planning"にある、それは業界、特に自動車の製品を開発するために使用される手順と技術のフレームワークです。.
複雑な製品やサプライチェーンは、特に新しい製品が発売されたときに、さまざまな失敗の可能性を示します。 APQPは、新しい製品やプロセスに対する顧客満足を保証することを目的とした、製品やプロセスの設計のための構造化プロセスです。.
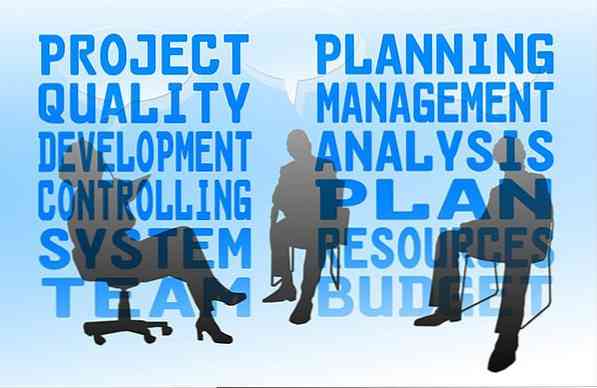
このアプローチでは、新製品やプロセスの変更に伴うリスクを軽減するためのツールと方法を使用しています.
その目的は、サプライヤが顧客を満足させる製品またはサービスを設計し、異なる活動間のコミュニケーションとコラボレーションを容易にすることを可能にする、製品品質要件の標準化された計画を作成することです。.
APQPプロセスでは、マーケティング、製品設計、購買、生産、流通を含む多機能チームが使用されます。このプロセスは、その製品開発システムのために、ゼネラルモーターズ、フォード、クライスラー、およびそのサプライヤーによって使用されます。.
索引
- 1フェーズ
- 1.1フェーズ1:プログラムの計画と定義
- 1.2フェーズ2:製品の設計と開発
- 1.3フェーズ3:製品製造プロセスの設計と開発
- 1.4フェーズ4:プロセスと製品の検証
- 1.5フェーズ5:立ち上げ、評価、および継続的な改善
- 2例
- 2.1 APQPを組み込む場所
- 2.2それを使う産業
- 3参考文献
フェーズ
APQPは開発プロセスの指針として、またサプライヤと自動車会社の間で結果を共有するための標準的な方法としても役立ちます。それは5つのフェーズで構成されています。
フェーズ1:プログラムの計画と定義
顧客の要求が新製品の導入または既存製品の改訂を要求する場合、製品の設計または再設計に関する議論の前であっても、計画は中心的なテーマになります。.
この段階では、計画は顧客のニーズと製品の期待を理解しようとします。.
計画活動には、クライアントが望むものを定義するために必要なデータを収集し、次にこの情報を使用して製品の特性を議論することが含まれます。.
その後、指定されたとおりに製品を作成するために必要な品質プログラムを定義できます。.
この作業の結果には、製品設計、信頼性、および品質目標が含まれます。.
フェーズ2:製品設計と開発
この段階の目的は、製品設計を完成させることです。これは、製品の実行可能性の評価が役立つところでもあります。この段階での作業の結果は次のとおりです。
- 完成したデザインのレビューと検証.
- 材料および機器の要件の定義済み仕様.
- 故障確率を評価するための完成設計の影響と故障モードの解析.
- 製品プロトタイプの作成のために確立された管理計画.
フェーズ3:製品製造プロセスの設計と開発
この段階では、新規または改良された製品を生産する製造工程の計画に焦点を当てます。.
目的は、製品の仕様と品質、および製造コストを考慮して製造プロセスを設計および開発することです。.
このプロセスは、効率を維持しながら、消費者の予想需要を満たすのに必要な量を生産できなければなりません。このフェーズの結果は次のとおりです。
- プロセスフローの完全な設定.
- リスクを識別して管理するためのプロセス全体の影響と障害モードの分析.
- 運用プロセスの品質仕様.
- 製品の包装および仕上げ要件.
フェーズ4:プロセスと製品の検証
これは、製造工程と最終製品を検証するためのテスト段階です。この段階の手順は次のとおりです。
- 生産工程の能力と信頼性の確認同様に、製品の品質の合格基準について.
- 試作ランの実現.
- 実施された生産手法の有効性を確認するための製品テスト.
- 次のフェーズに進む前に必要な調整をしてください.
フェーズ5:立ち上げ、評価および継続的改善
この段階では、プロセスの評価と改善に重点を置いて、大規模生産の開始が行われます。.
このフェーズの柱の中には、プロセス変動の減少、問題の特定、そして継続的改善を支援するための是正措置の開始があります。.
プロセスの効率化と品質計画に関連する顧客からのフィードバックやデータの収集と評価もあります。結果は次のとおりです。
- プロセス変動を減らすことにより、より良い生産プロセス.
- 製品の納入品質と顧客へのサービスの向上.
- 顧客満足度の向上.
例
APQPを組み込む場所
- 品質機能の実装を使用して、クライアントの声からの要件の開発.
- プロジェクトスケジュールに統合された製品品質計画の策定.
- 設計を発表する前に、特別な特性やキーをプロセス設計活動に伝達する製品設計活動。これには新しい形状と部品、より厳密な公差と新しい材料が含まれます.
- テスト計画の策定.
- 進捗状況を追跡するための正式な設計レビューの使用.
- 製品設計の元から与えられた設計公差に従って、プロセスの適切な機器とツールの計画、入手、設置.
- 製品をより良く組み立てる方法に関する組立および製造担当者による提案の伝達.
- まだ潜在的な失敗の危険を冒す、製品の特殊な特性やキーまたはプロセスのパラメータに対する適切な品質管理の確立.
- 現在の変動を理解し、プロセスの統計的制御とプロセスの能力を使って将来のパフォーマンスを予測するための、特別な特性の安定性と能力の研究の実現.
それを使う産業
フォードモーターカンパニーは、1980年代初頭にサプライヤー向けの最初の高度な品質計画マニュアルを発行し、これによりフォードのサプライヤーは新製品に対する適切な予防および検出管理を開発することができ、これにより企業の品質への取り組みを支援.
80年代の終わりには、自動車業界の主要メーカーがAPQPプログラムを使用しました。ゼネラルモーターズ、フォードとクライスラーはそれを実行して、そしてそれから彼らの供給者のために製品品質計画原則の共通の核心をつくるために団結する必要性を見ました.
このガイドラインは、APQPプロトコルが標準化されたフォーマットで行われるようにするために1990年代初頭に制定されました。.
自動車業界内で相互に関心のあるトピックについて共通の理解を得るために、3つの自動車メーカーの代表者とアメリカ品質管理協会は、一連の品質要件を作成しました。.
この方法論は、計画を通じて品質とパフォーマンスを保証するために進歩的な企業によっても使用されています。.
参考文献
- ウィキペディア、フリー百科事典(2018)。高度な製品品質計画撮影元:en.wikipedia.org.
- NPDソリューションズ(2018)。高度な製品品質計画撮影者:npd-solutions.com.
- クオリティワン(2018)高度製品品質計画(APQP)撮影者:quality-one.com.
- 餌(2018)。 APQPの5つのフェーズ:主な要件の概要撮影者:cebos.com.
- デビッドイングラム(2018)。高度な製品品質計画スモールビジネス - Chron.com撮影元:smallbusiness.chron.com.